The eco-design of our containers
Eco-design is defined by the Ademe (Environment and Energy Management Agency) as the development of a product using as few non-renewable resources as possible, preferring the use of non-renewable resources. renewables, operated while respecting their renewal rate and associated with waste recovery that promotes reuse, repair and recycling.
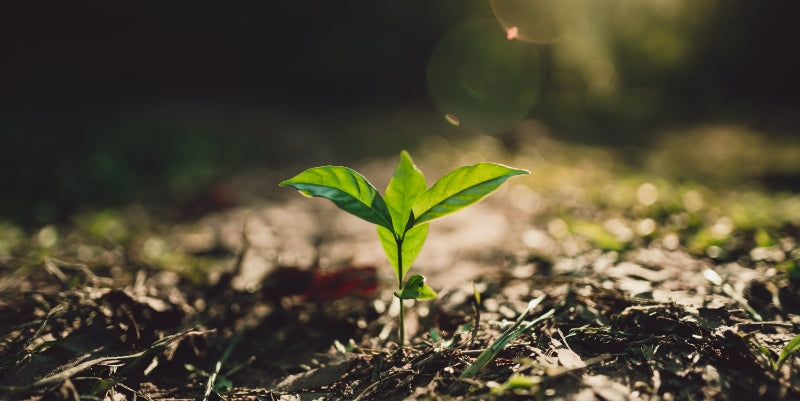
Is there an ideal container for cosmetics?
The answer, as you can imagine, is obviously no!
During the design and redesign of our visual identity, we carried out eco-design work on our products and therefore on their life cycle. You will find below the main steps that allowed us to make choices that seem to us to have the least impact on our environment, but if when reading this page you think you have suggestions for further improvement, we are all ears.
Container development
To have the best chance of making the best trade-offs in the choices that arise when designing containers, it seemed important to us to start by defining the exact role of the container in this first step. Because it is quite often possible that the most obvious choice could be total heresy from an environmental point of view.
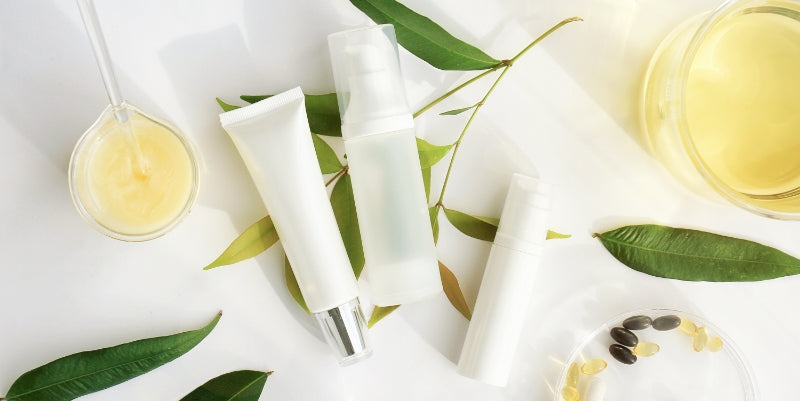
Step 1 - Define the role of the container
Containing the product : to protect it of course... a cosmetic cream is an emulsion between an oily phase and an aqueous phase. It is therefore essential to have a container that properly protects the product.
Communicate : give the name of the product and indicate the legal information (INCI), advice for use , etc. The container is therefore the first communication medium for the product. It provides information on its composition and its benefits.
Facilitate its use : the container must provide additional ease of use, and make it possible to optimize its use to save money during use and avoid waste.
Is it better for our environmental impact to import glass containers made in China? or aluminum produced in India? or plastic injected in Italy?
And what are the manufacturing processes and their direct impacts in terms of releases?
~~~~~
Selection of lower impact materials
The different materials used for cosmetic containers are essentially plastic, glass and, more marginally, aluminum. It is therefore necessary to take into account the necessary raw materials as well as the difficulties of taking them from nature and their abundance to understand the real impacts on our environment.
And define the embodied energy of the container, that is to say the energy it will have taken to extract the raw material, transport it to the place of production, the energy and the polluting discharges then, the energy it took to get to you.
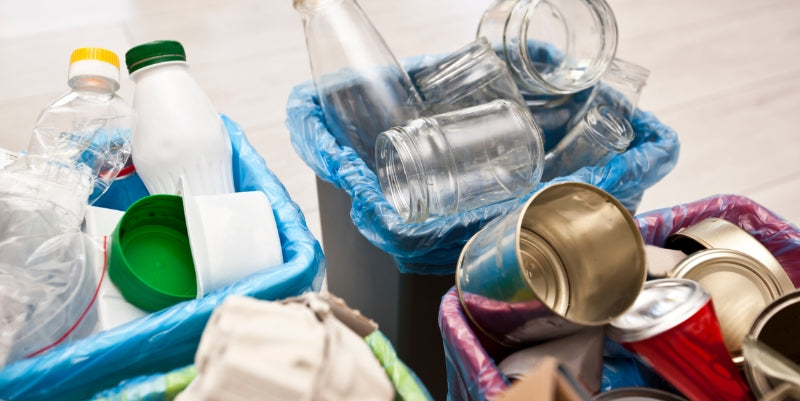
Step 2 - Define the material
Plastic : from naphtha which is a transparent liquid obtained after distillation of petroleum, this liquid is essential in the manufacture of plastic. It is condensed between 180°C and 40°C. It then undergoes a so-called “cracking” stage to obtain small molecules called monomers, which will react to form chains of plastic polymers. But it is light, flexible, unbreakable and hygienic and offers plenty of recycling outlets.
Glass : this is the material that seems the most natural, especially since it is very well collected and therefore almost 90% recycled in France. But it requires silica sand and dolomite, a subject that seems trivial but unfortunately sand, especially rich in silica, has become an overexploited resource in the world and with dredger boat techniques sucking up sea sand having a strong impact on the seabed.
Aluminium : the production of this metal from bauxite gives rise to significant pollution, including an emission of fluorine which escapes into the air and water, notably attacking vegetation when it is melted at about 950°C. The production of aluminum also generates red mud, that is to say impurities rich in alumina and iron hydroxide which give it this color. Finally, aluminum is a resource that is also tending to become scarce.
Maximize the use phase
The container should provide a good user experience. As we have seen, he must first of all protect the product but, in cosmetics, he must also deliver it, this avoids having to dose with the finger directly into the product. An Airless type bottle can offer more than 250 doses for a 50 ml container.
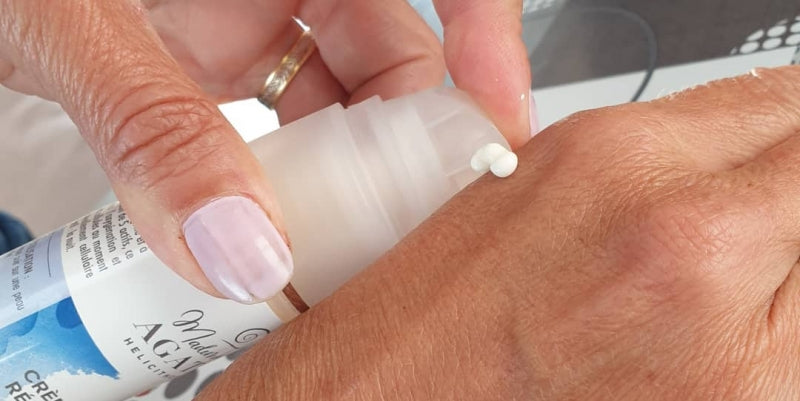
Step 3 – The user experience
We opted for a bottle with an Airless-type dispenser pump.
The Airless system protects the cream from contact with the outside air. This pump system raises a piston from the bottom of the bottle, which allows all of the cream to be used without wasting anything.
The Airless system offers the advantage of a correct dosage of the product. Only this pump allows to obtain more than 250 doses of hydration delivered without any waste.
For communication we have chosen to use a label rather than hot stamping or screen printing directly on the container. Thus the label allows a large number of details and we opted, during our change of visual identity, for white as the majority color. So we use as few colors as possible to facilitate recycling possibilities.
Optimization of logistics
The choice of plastic rather than glass comes mainly from logistics, indeed for a very local system with the user who moves with his glass container to the producer, it is the glass that has the least impact, but if it is shipped then the glass requires 5 times more means of transport because of its weight.
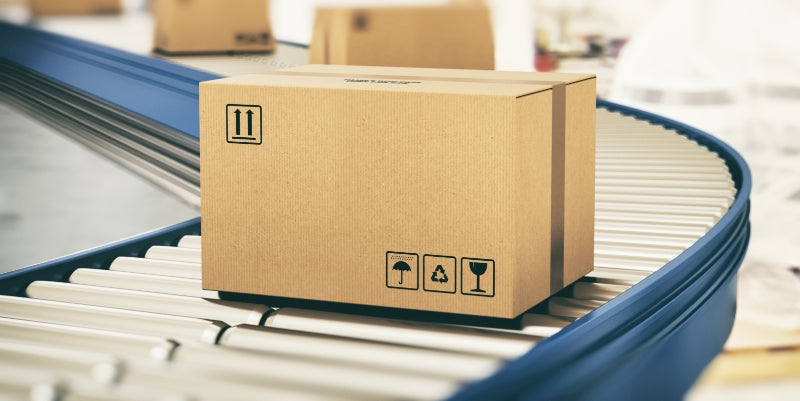
Step 4 – A heavy logistics cycle
Logistics takes an important place in the eco-design of our care since more than 50% of our annual turnover is made on our website.
So we have a very large shipping and logistics position. It is therefore crucial that storage and shipping are factored into our impact.
Another example, labeling rather than screen printing is an important logistical choice because we can manage the supply of containers only according to their capacity and not their formulations.
In fact, hot stamping CREAM DAY on a container can no longer become a CREAM NIGHT. The label allows for greater flexibility. Less storage, less transport and less waste.
Finally, cosmetics regulations change very often, if we have to comply with new rules, we just have to change the labels.
A bit like the Shadoks, it instinctively seems quite inefficient to manufacture single-use glass containers to recycle them in a wireframe that will re-manufacture single-use glass containers. It seems more important to clearly define the industrial recycling options that will offer a large number of outlets for our plastic containers.
~~~~~
Product end of life management
The plastic recycling rate was in 2020 according to a Citéo/Adelphe report of 54.5% and 85% for glass. We therefore quickly understand that the real problem with our plastic containers is to ensure that they are recycled.
For this reason, we have set up a free return of used containers. We have identified a partner in the Loiret who carried out an identification phase of our plastics to ensure an upgrading in textiles, insulation or even vehicle dashboards.
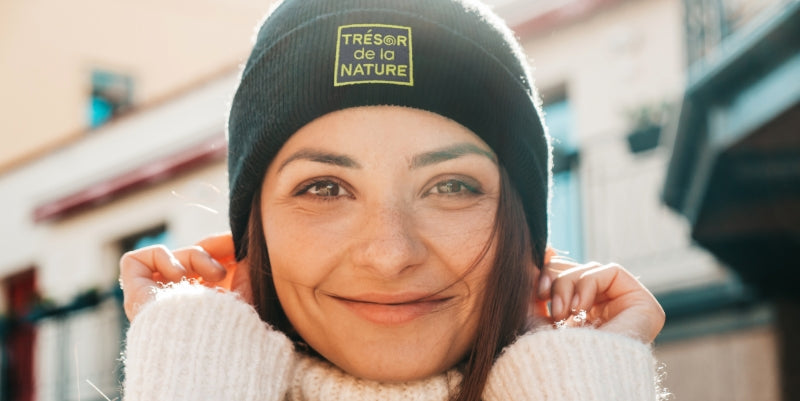
Step 5 – Secure outlets
Our recycling program for our containers is divided into 4 phases:
PHASE 1 : CUSTOMER COLLECTION
We initially propose to store our used containers to accumulate at least 5 of them. Then you have to take a photo of the containers, send it to us and then we send a prepaid label to stick on the package. So the return is free, but it is our customers who are the most important.
PHASE 2 : IDENTIFICATION, SORTING & SHREDDING
When we receive the containers, we collect them to ship them to our partner. You must have collected the equivalent of a full pallet to be able to ship it. The containers are then crushed into large shavings to be sent to the recycling plant and thus further reduce their volume.
PHASE 3 : RECYCLING AND GRANULATION
The chips are then washed to remove all impurities from the first use. Once clean, you have to go through the granulation phase. The granulation will make it possible to find a reusable raw material for a new industrial use. Bales of pellets are then shipped to different sites based on supply and demand.
PHASE 4 : USES (Synthetic Wadding, Textile, Insulation). We have been able to identify several manufacturers who use these granules to make Synthetic Wadding in the textile industry or in the insulation of homes. But other uses are possible, such as revaluation as a children's play area slab, or even as a car part. The important thing is that we have the assurance that your returned containers will indeed be recycled in a circular and respectful economy.
We count on you !
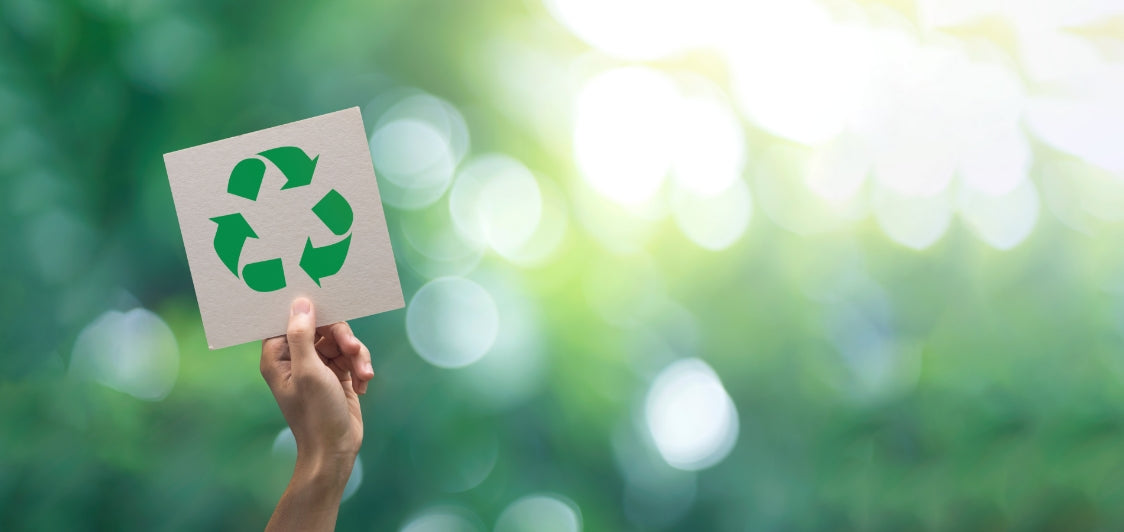
Recycle your containers
It seems today that most consumers are ready to reduce their environmental impact, to do this, the choice of recycling has become essential. So it is essential to offer our customers a reliable solution by returning their used containers to us so that we can ensure that they will not end up incinerated but in a recycling chain with a large number of outlets such as textiles, insulation or even car bumpers.
See recycling